Energy contributes over 40% of New Zealand’s total greenhouse gas emissions. One third of these are from process heat, that in most instances is generated from burning fossil fuels. Process heat is mostly used by industrial businesses, providing a unique opportunity for industry to contribute significantly to our goal to reach net zero carbon emissions by 2050.
Heat pumps provide a low-carbon alternative to fossil fuels for industrial process heat.
Industrial heat pumps
- Heat pumps are suitable for businesses with heat temperature requirements below 100 degrees.
- Heat pumps are recommended for industrial sites with hot water requirements such as dairy product manufacturing, meat product manufacturing, and food and beverage manufacturing.
- If designed well, a heat pump can have high co-efficient of performance (COP) which means that operating costs are around 45% to 75% of a natural gas or coal boiler.
- The high efficiency associated with heat pumps can significantly reduce or even eliminate the need for a network connection upgrade.
On this page:
- What are industrial heat pumps?
- What industries are heat pumps suitable for?
- Benefits of heat pumps
- How businesses are using heat pumps
- Is a heat pump the right option for your business?
- Breaking down the costs
- When are heat pumps not recommended?
- Heat pumps over 100°C
- Other considerations
- Prep for success
What are industrial heat pumps?
Heat pumps are high-efficiency heat sources that upgrade ambient or waste heat to useful temperatures by using relatively small amounts of electricity. Industrial heat pumps are designed to meet industrial process heat loads and operating requirements and are emerging as key tools to decarbonise industrial process heat.
An industrial heat pump is generally larger and higher capacity than a residential or commercial heat pump and will generally be designed for higher operating load factors, output temperatures and reliability. Additional features such as instrumentation, control systems and hazardous environment compliance may be present.
How does a heat pump work?
Electric heat pumps use a vapour compression cycle with a refrigerant working fluid. The low-pressure refrigerant absorbs heat from a low temperature source (ambient air or a waste heat stream). It is then compressed which raises the temperature to the target level, and heat can be extracted via a heat exchanger. This process can supply heat more efficiently than heating the fluid through conventional means (e.g. a fossil fuelled boiler).
Heat pump characteristics
- High temperature heat pumps — Heat pumps that can reach temperatures greater than 60°C are usually custom designed for particular applications such as heating (e.g. used for cooking, blanching and melting), cleaning in place, drying/evaporation and sterilisation/pasteurisation. Currently, available heat pumps are generally limited to temperatures below 100°C, which makes them suitable for producing hot water, but not steam. Although not widely available (including in New Zealand), output temperatures of up to 150°C can be achieved if waste heat of about 100 °C is available as input. For temperatures between 150 °C and 200 °C, heat pumps need special refrigerants and compressors, for which technologies are still in an early prototype stage. Research that is currently underway shows that temperatures of industrial heat pumps have the potential to reach temperatures greater than 200°C.1
- Low temperature heat pumps — Low temperature heat pumps can use ambient air to reach 60-65ºC quite readily, and are typically generic, off the shelf products. To reach higher temperatures, alternative refrigerants, compressors and often multiple stages are used, which impacts on cost and performance.
- Heat source efficiences — Industrial heat pumps often utilise waste heat or low-grade heat resources as heat sources e.g. heat released from processes such as refrigeration. This achieves higher performance efficiencies by using higher source temperatures than ambient heat pumps and may also allow better integration and a smaller size. Integrating heat pumps with industrial refrigeration systems to use waste condenser heat as a heat source can work particularly well as it may benefit both systems. Correct integration is important in getting the optimum performance from the heat pump.
1International Energy Agency: The Future of Heat Pumps(external link)
Businesses across multiple industries have already made the shift from fossil fuels to electric heat pumps. Making the switch may be the right move for your business too.
What industries are heat pumps suitable for?
Industrial heat pumps are gaining popularity both internationally and here in New Zealand to provide process heat needs across different industries, including:
- dairy product manufacturing
- meat product manufacturing
- food and beverage manufacturing
- wood product manufacturing
- textile, leather, clothing and footwear manufacturing
- indoor cropping
- agriculture.
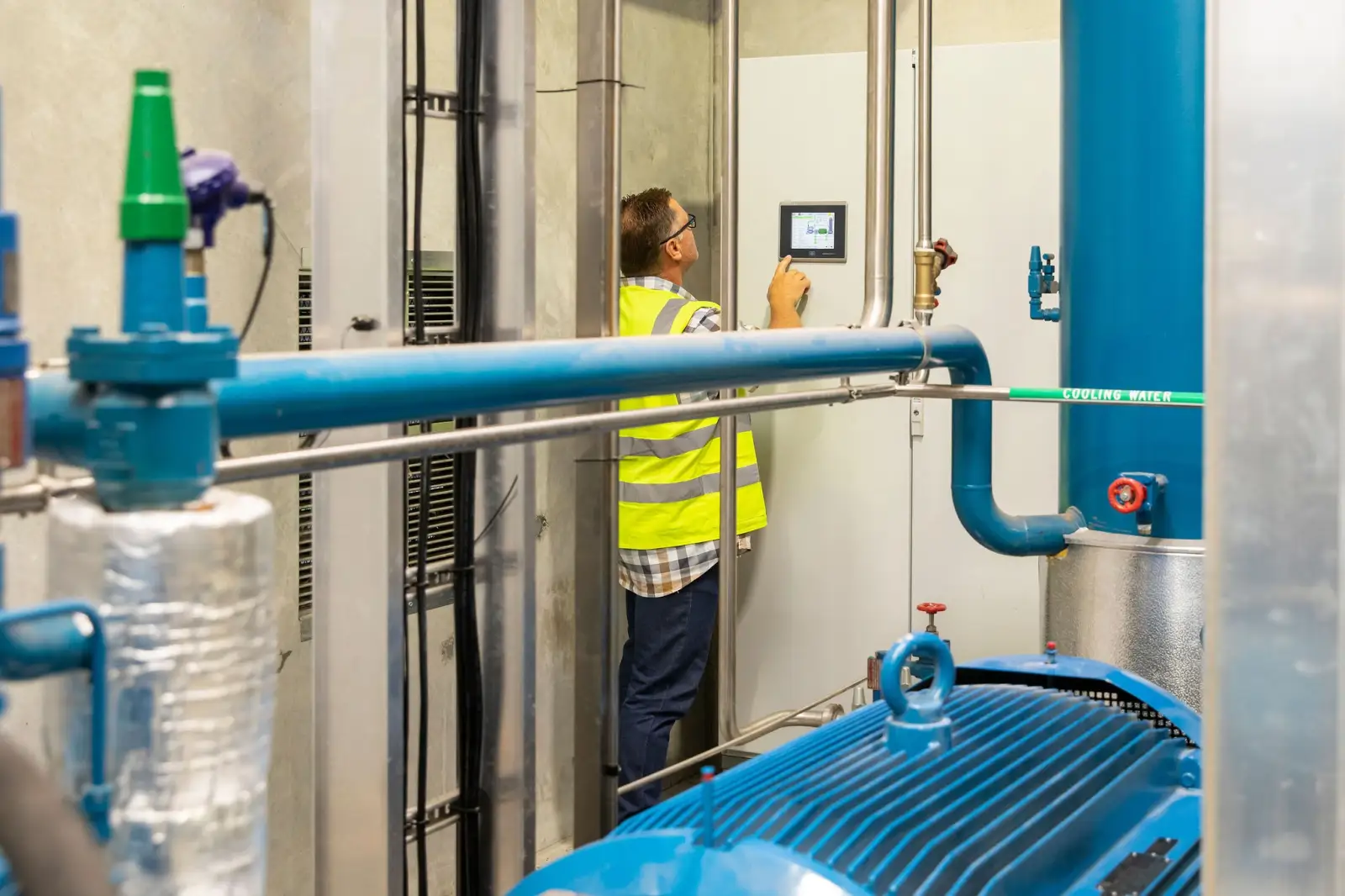
Benefits of heat pumps
Heat pumps have multiple advantages over fossil fuel boilers.
- Highly efficient and low carbon emissions — Heat pumps have high coefficients of performance (COP) of 3.0 to 5.02 (fossil fuel boilers typically have a COP of 0.75 to 0.95), which combined with New Zealand’s low carbon electricity generation enable a very low-carbon way of generating heat with none of the losses of combustion processes.
- Convenience and cost — Heat pumps are compact, easily installed, and they avoid boiler house costs; heat pumps can often use existing electricity supplies when retrofitted.
- No products of combustion — Electrically driven high temperature heat pumps have no emissions (e.g. no products of combustion to dispose of such as ash or flue gases including NOx and SOx, and no coal dust) and are cleaner to operate than a boiler-based heating system. Therefore, they typically do not require resource consent.
- Safe and highly durable — Heat pumps are reliable. They contain proven components and built-in controls to self-regulate their operation.
- Highly-responsive — Staged compressors and variable speed drives offer rapid load response and good turndown control.
- Lower maintenance — Component degradation rates are lower for heat pumps due to lower component temperatures meaning that less maintenance is required.
- Smaller physical size — Fuel storage is not required. This may greatly reduce the physical size of the heating system compared to a fossil fuelled alternative. Multiple heat pumps can be distributed around a site (if the site is suitable) close to the heating demand, reducing distribution network heat-losses and improving heating system efficiency.
- Future proofing — Future power grids will require more rapid responses to changes in demand; heat pumps can offer cost-effective demand response capabilities.
Heat pump leads to savings at Silver Fern Farms
Switching away from coal has benefits from a carbon reduction and cost saving point of view.
"The benefits are substantial and include reductions in our coal consumption, the associated reduction in greenhouse gas emissions and cost savings as the heat pump system generates hot water at a lesser running cost than coal boilers, and reduction in remaining water heating loads, opening up a variety of possibilities to achieve the final water heating we need."
Kate Beddoe, Chief Sustainability and Risk Officer from Silver Fern Farms.
ANZCO project: industrial heat pump installation
ANZCO Foods has a mission to become the world’s most environmentally responsible red meat producer. The latest step in this journey has been focusing on decarbonisation, specifically, reducing coal usage at ANZCO’s largest site in Canterbury through the installation of an industrial high temperature heat pump.
ANZCO engaged energy and sustainability consultancy DETA to identify how a high temperature heat pump could be implemented, including how to best integrate it into a brownfield site with minimal impact on production. To support the implementation, DETA connected ANZCO with the (now discontinued) Government Investment in Decarbonising Industry (GIDI) fund.
In Early 2021, co-funding was awarded to ANZCO to install the industrial high temperature heat pump at their Canterbury site. EECA and DETA teams worked alongside ANZCO and other suppliers including Active Refrigeration, Bradfords and SWARM Intelligence to deliver this project.
Key project stats
- Project title — ANZCO Canterbury Beef Processing Plant High Temperature Heat Pump
- Project location — Ashburton
- Heat pump capacity — 1MW
- EECA co-funding — $400,000 through the Government Investment in Decarbonising Industry (GIDI) fund.
- Estimated emissions saving — 3,080tCO2 per year
- Commission date — March 2022
Results for this project are due mid-late 2023. ANZCO expects their heat pump to robustly supply process heat to its plants, while significantly reducing emissions and overall costs without compromising quality or reliability.
Is a heat pump the right option for your business?
Adopting industrial heat pumps for process heat may be a good move for you if some or all of the following apply to your business:
- You are after a way to efficiently generate process heat that has a lower operating cost than traditional fossil fuel boilers.
- You require low-to-medium temperature process heat (less than 100°C).
- You are looking at ways to decarbonise your business as there are significant carbon emission reduction opportunities from using heat pumps in process heat intensive industries.
- There is available capacity in electrical infrastructure to support the switch to industrial heat pumps.
- You have space restraints and are unable to fit a boiler house and/or fuel handling system on site.
- You are looking at adopting a new solution (rather than converting a fossil fuelled boiler to a biomass or electric boiler).
- You are looking for a mix of heat pumps and electric/ biomass powered boilers to give you greater energy security or flexibility and lessen site fuel requirements.
- There is a waste heat source available at your site for high temperature heat pumps.
- Biomass is not a viable option for you, e.g. if there isn’t local supply.
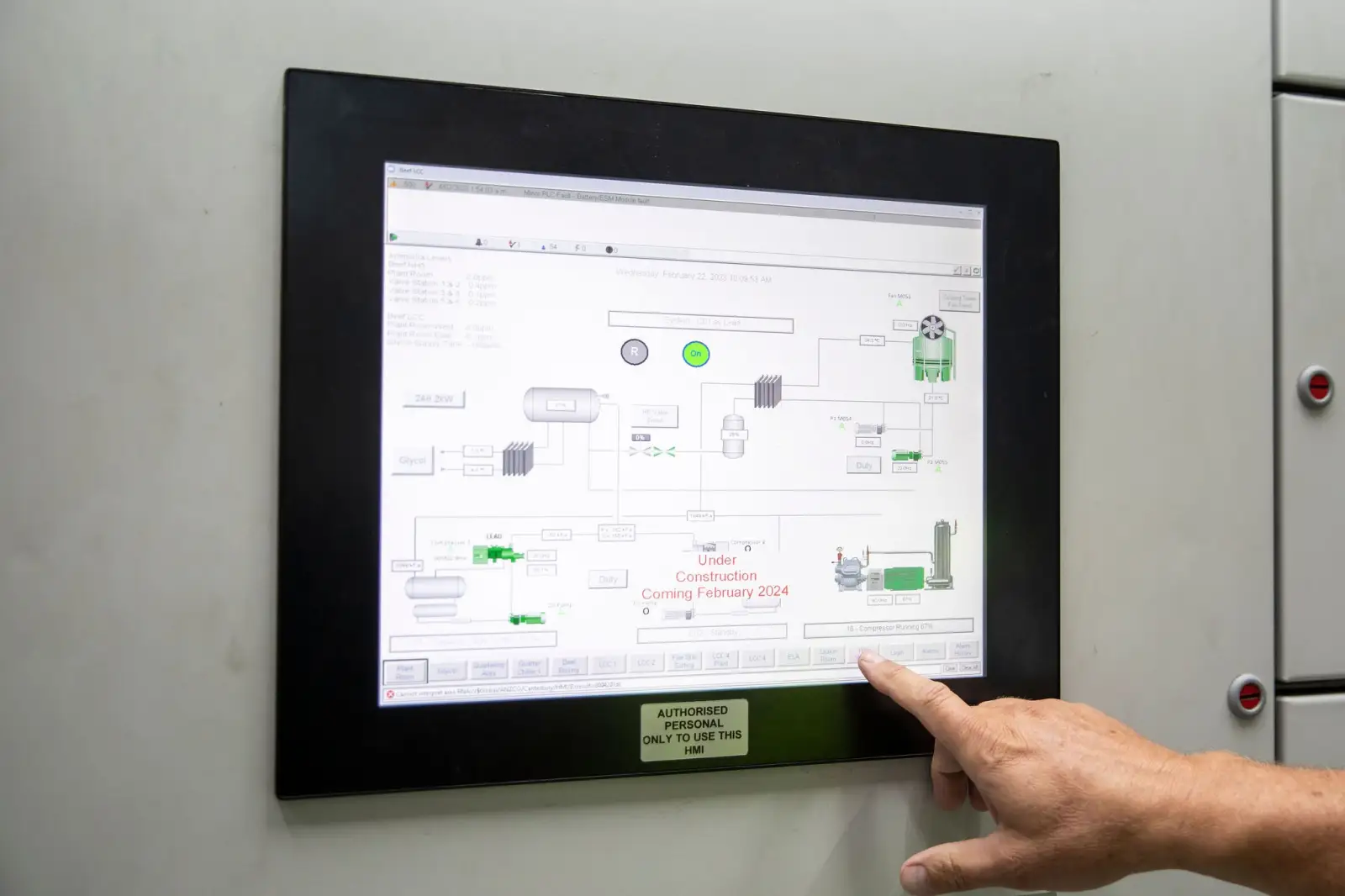
Breaking down the costs
While installing a heat pump will be an upfront cost to your business, there is significant potential to save costs in the medium-long term. There are also other hidden cost savings that businesses should consider when determining whether the switch is right or not.
Capital cost
- In general, a heat pump is likely to have a capital cost similar to a new biomass or coal boiler, and higher than new gas, liquid fuel, or electrode boilers. Typical capex costs from EECA co-funding applications between 2021-2023 were between $1million and $3 million per MW. This wide range reflects the fact that sometimes switching to heat pumps will create additional capital costs, such as network upgrades and heat recovery equipment.
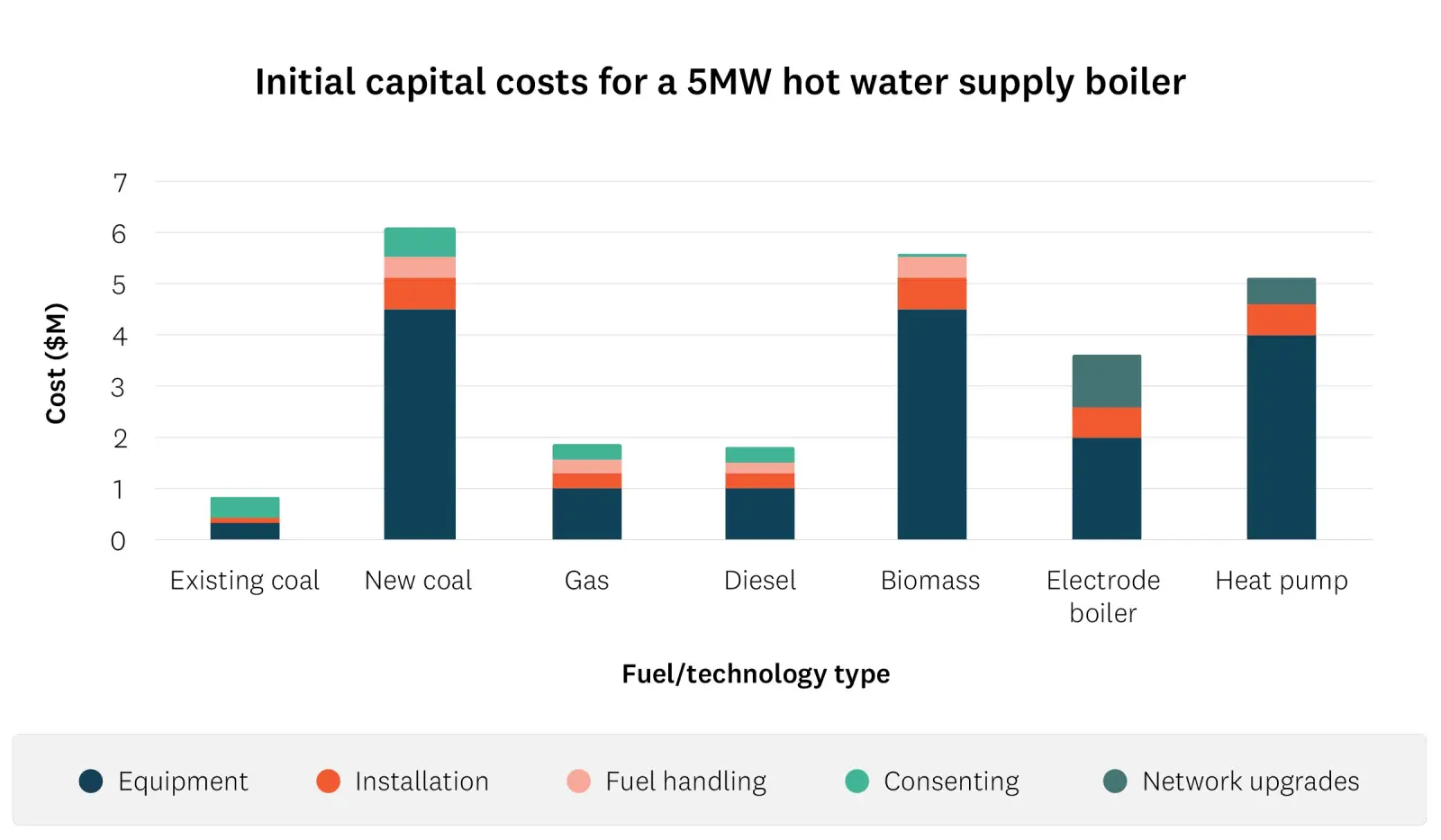
Running costs
- This extra capital cost is offset by energy cost savings in the medium-long term – typically a heat pump will deliver heat energy between 300% and 500% of the supplied electrical energy. What this means is that heat pumps are highly efficient at transforming electricity into heat.
- For example, if electricity is $0.15 per kWh and the heat pump has a COP of 4.0, and natural gas for an 80% efficient gas boiler is $15 per GJ, then the energy costs to run the heat pump will be around 55% of those to run a gas boiler.
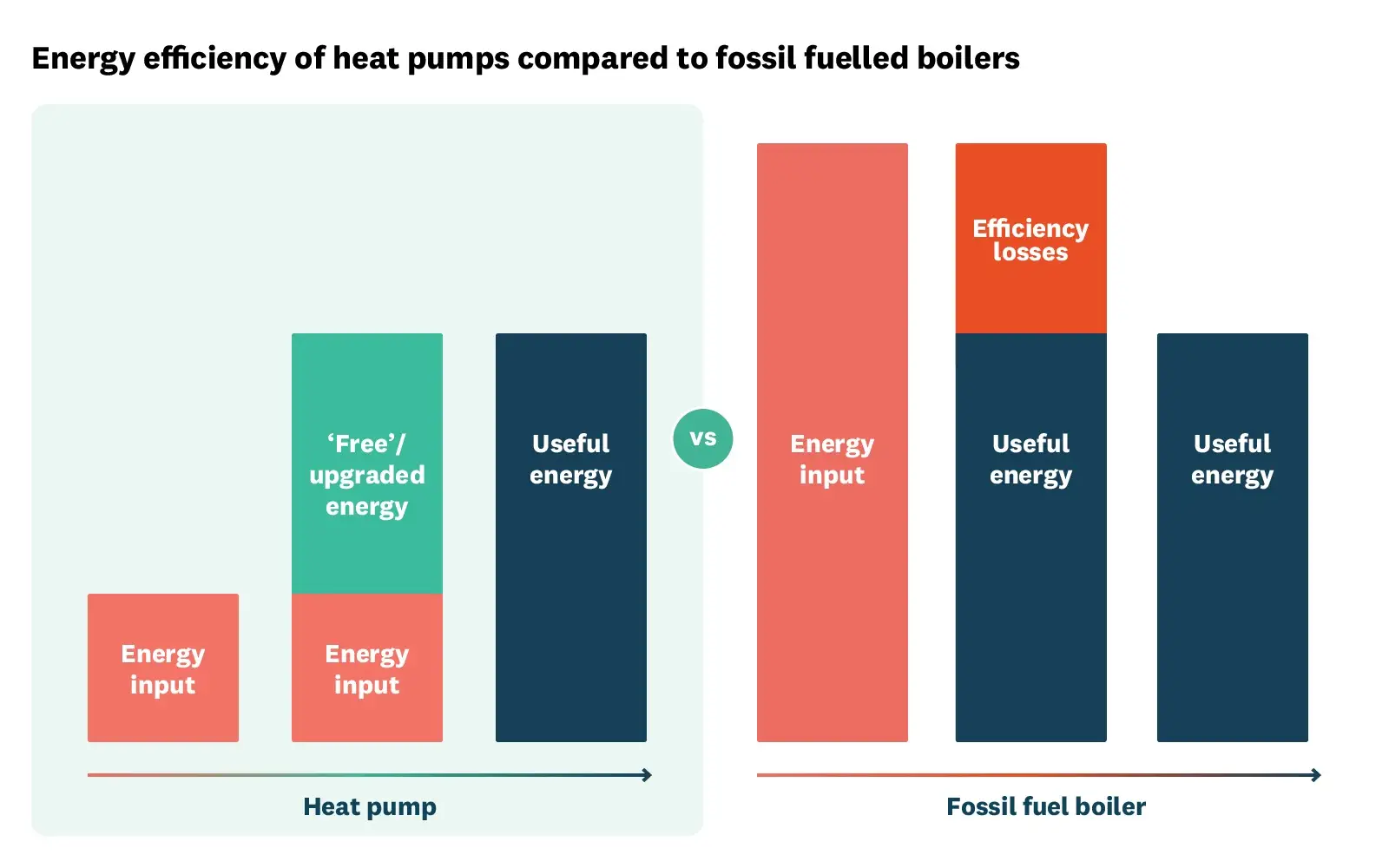
Other cost considerations
- A heat pump will use less electricity than an equivalent electrode boiler.
- Gas connection charges can be quite significant so if your site is removing gas altogether there could be additional savings.
- The high efficiency associated with heat pumps can significantly reduce or even eliminate the need for a network connection upgrade when compared with installing an electric boiler.
- A heat pump will generally reduce carbon emissions from heat delivered by 85 to 95%, depending on efficiency and the fuel replaced. With current New Zealand Emissions Trading Scheme prices at $85 per tonne of carbon dioxide, the heat pump projects co-funded by EECA between 2021 and 2023 will reduce their businesses’ emissions trading scheme liability by an average of $300,000 per year.
- Heat pumps don’t require ash disposal, fuel handling and other such operational costs, and may require less supervision and operator intervention.
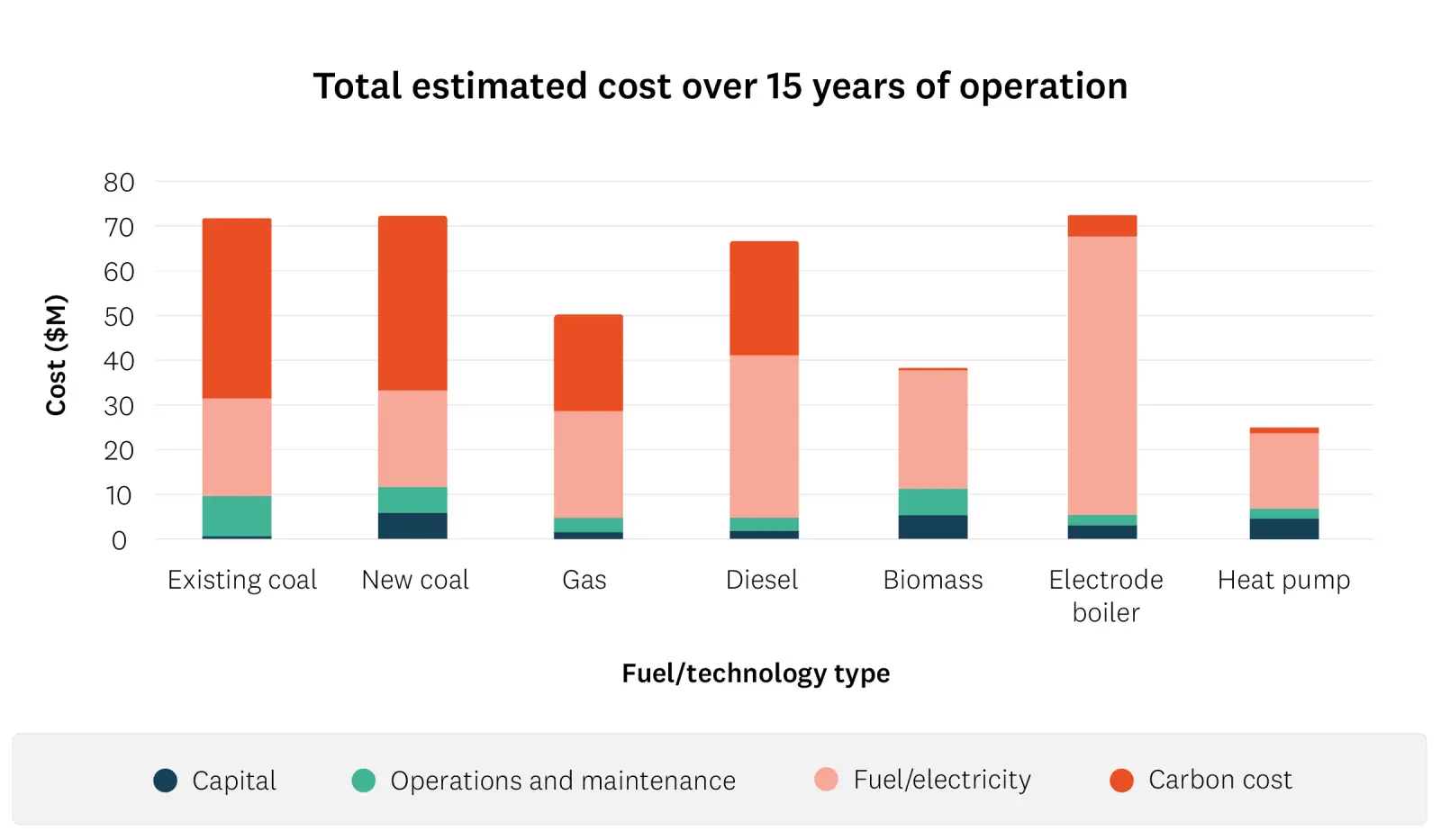
The initial investment can certainly be a hurdle to overcome, but we have found that our operating costs have reduced, and by making the move earlier we can contribute far more to the 2050 emissions reductions targets.
When are heat pumps not recommended?
While there are many advantages to adopting heat pumps for industrial process heat, there are also potential challenges or circumstances where an alternative solution may be better for your business.
Some challenges with industrial heat pumps include:
- High temperature process heat applications — Today, industrial heat pumps are mainly used for low‐temperature processes below 100°C. Temperatures above this would be better suited for a biomass or electric boiler.
- Network charges — Capacity, time of use and peak demand charges may mean that heat pumps incur significant costs during certain periods. It may make sense to use heat pumps alongside non-electric water heaters, or with thermal storage for use during peak-electricity demand periods and to increase system resilience. Variable speed control can also allow the electrical demand of the heat pump to be temporarily lowered in times of high site or network electrical demand, to respond to electricity tariff rates or participate in demand-response programmes.
- Electricity supply requirements — Industrial heat pumps typically draw around a quarter to a third of the equivalent thermal load as electricity so they may require an increase to a site’s electricity supply capacity. Cabling and switching equipment on-site can be expensive - especially for longer distances.
- Heat source quality — Heat pumps require reliable heat sources for efficient operation. The closer the heat source is to the output temperature, the higher the efficiency. Air source heat pumps can suffer reduced performance and output during cold weather.
- Complexity — High temperature heat pump systems can be technically complex and may be expensive to design and install. Maintenance staff may need upskilling on the new technology.
- Low utilisation factors — A heat pump is a high capital cost item, so if your utilisation factors are low, the energy and carbon savings might not be high enough to recover the capital cost.
Heat pumps over 100°C
EECA is currently seeking proposals from New Zealand businesses for very high-temperature heat pump projects to demonstrate the technology here.
The tender closes 12 December 2024.
Seeing the project team overcome some of the challenges that were identified during this project’s delivery is a testament to how we can work collaboratively with our project managers and contractors, to deliver real change.
Prep for success
If you are thinking of switching to heat pumps for industrial process heat, it is important that you undertake your own research and take all relevant steps to best set yourself up for success.
It is normal for businesses to face barriers when adopting clean process heat technology. Several large businesses that have adopted these technologies have identified a range of lessons that other businesses can learn from. Work commissioned by EECA through the University of Waikato has found the following learnings from businesses that have installed industrial heat pumps, that may serve as a guide for future energy decarbonisation projects based on heat pump technology. The learnings from the reviews are organised into 5 key steps:
1. Understand the process mass and energy balance and constraints
The first step in any energy and emissions reduction study should be to map the current situation comprehensively. Formulating a high-quality mass and energy balance of specific processes or the site is essential to all subsequent steps. If the mass and energy balance step is not sufficiently carried out, it results in a much riskier project with limited basis to model and predict the value of installing an industrial heat pump. Where this has been the case, sites have needed to return to re-doing their mass and energy balance, stalling progress on the heat pump project, and incurring new costs.
2. Minimise process demand for heating and cooling
Often, the most effective way to minimise emissions is to minimise the demand for process heating and cooling. Low-hanging fruit such as insulation, minimising hot water to drain, tuning an existing utility plant, and heat recovery are standard, tried, and true measures that should be implemented before considering heat pumps. Mass and energy balance analysis, process analysis, and pinch analysis all play essential roles in gaining the required insights to minimise thermal demand.
3. Heat pump integration analysis and preliminary costing
This step looks at the placement and size of the heat pump regarding the sources of low-grade heat to produce the required high-grade heat. Pinch analysis can clearly show the appropriate integration design and arrangement of multiple heat pumps to maximise system COP, which produces a more favourable economic outlook. At this stage, a preliminary costing of the project (e.g. Class 5 - order of magnitude) should be undertaken to determine project viability.
4. Heat pump selection and cycle design
The next step is to ensure appropriate selection of heat pump and its cycle design. Industrial heat pumps are commonly ammonia or CO2 refrigerant based because they offer high COP values and require relatively low swept volumes (due to high volumetric heating capacities). In the future, hydrocarbon refrigerants (such as butane) may also become popular in heat pumps that operate above 100°C to expand the range of process heating potential. Modern HFO refrigerant-based heat pumps have also been developed, although these are currently targeted towards the commercial and residential markets. Sites that have limited experience with ammonia heat pumps may consider alternative refrigerants that are less toxic, such as modern HFO, CO2 or other natural refrigerants.
At the industrial scale, ammonia heat pumps are the most well-established type of heat pump.
5. Full business case development
The development of a full business case based on the system design is integral to the success of a heat pump project. A key challenge in determining the economics of a business case is the New Zealand Emissions Trading Scheme (ETS) carbon price and the electricity price to use. Most EECA co-funding applicants used forecasted NZ ETS values from the Climate Change Commission. For electricity price assumptions, most applicants use their current electricity price or discuss future electricity prices with their provider based on the additional electrical capacity required for a heat pump.
EECA developed a business case checklist for co-funding applicants that may be helpful for your business if you are planning on investigating installing an industrial heat pump.
Business Case Checklist [PDF 2.7 MB]
The Large Process Heat Users and Energy Efficiency in New Zealand report, commissioned by EECA and prepared by Price Waterhouse Coopers New Zealand, also outlines barriers that businesses both in New Zealand and in the international context have faced, as well as ways these barriers have been overcome.
Regional Energy Transition Accelerator
EECA is working with local stakeholders through its Regional Energy Transition Accelerator (RETA) programme to identify the best decarbonisation options for each region, starting with South Island regions in 2022/23.
Keep reading
-
Red meat, green energy
Alliance Group installed New Zealand’s first high temperature heat pump, commissioned in 2019 at its Nelson plant. Within its first year of operation diesel use was reduced by 44% and on-site electrical efficiency was improved.
-
Cutting coal and carbon emissions at Silver Fern Farms
Silver Fern Farms installed a high temperature heat pump to preheat hot water for the processing plant, shifting heating load away from the existing coal boiler.
-
Heat is on to find alternative energy sources
Goodman Fielder is trialling an energy efficient alternative at its dairy factory in Palmerston North with the support of government funding.