Despite New Zealand dairy farms having the world's lowest carbon footprint, agriculture still accounts for almost half of the country’s greenhouse gas emissions. Goodman Fielder is one company in the dairy industry committed to more sustainable practices.
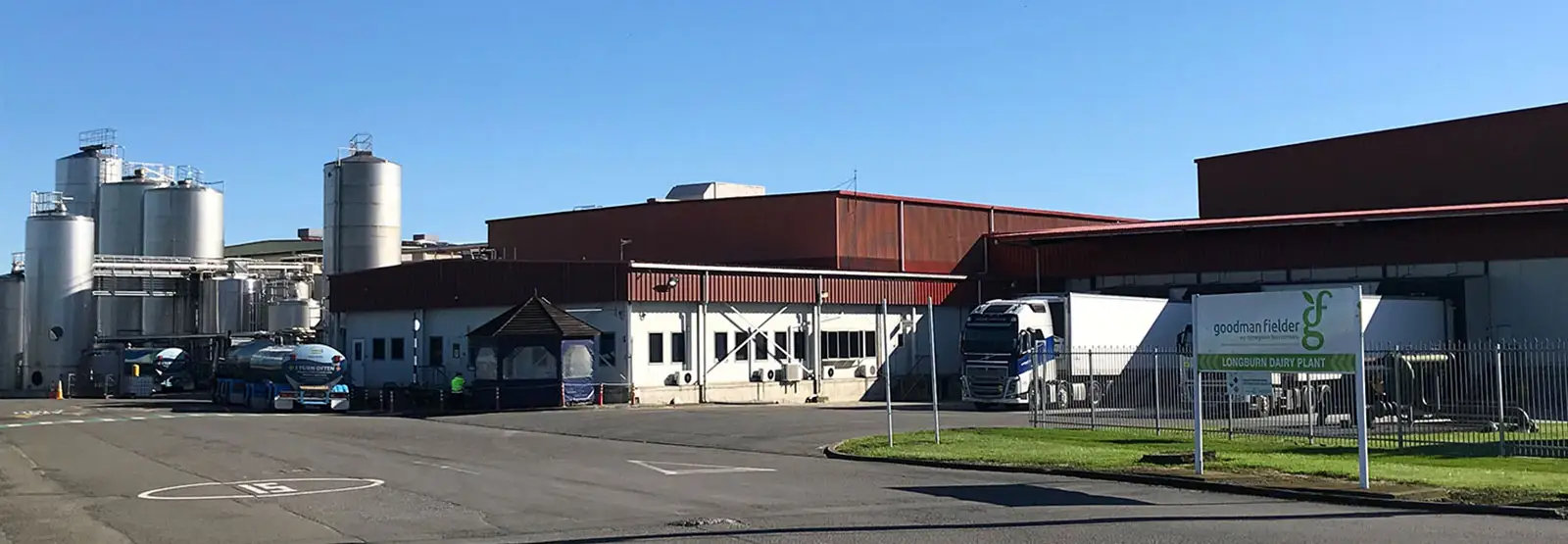
As part of their investment in alternative energy sources, the company is reducing the amount of natural gas used in the boilers at their Longburn dairy factory in Palmerston North, with a high temperature ammonia heat pump to capture and reuse waste heat from refrigeration compressors.
The project is part-funded by EECA (Energy Efficiency and Conservation Authority) through the Government Investment in Decarbonising Industry initiative (GIDI Fund). It’s one of 14 successful project applications to the first round of the GIDI Fund with the government committing almost $23m in co-funding to help businesses transition away from fossil fuels.
"GIDI funding helped justify choosing a heat pump over a new gas boiler," says John Kennedy, National Engineering Manager with Goodman Fielder. "A new gas boiler was by far the cheapest capital expenditure option but the heat pump is a more sustainable choice. As part of an EECA-supported feasibility study, we found the capacity of our gas boiler was pretty well 'tapped out'. Instead of putting in a new gas boiler we looked at alternative technologies to reduce the load on our boilers, and reduce our carbon emissions."
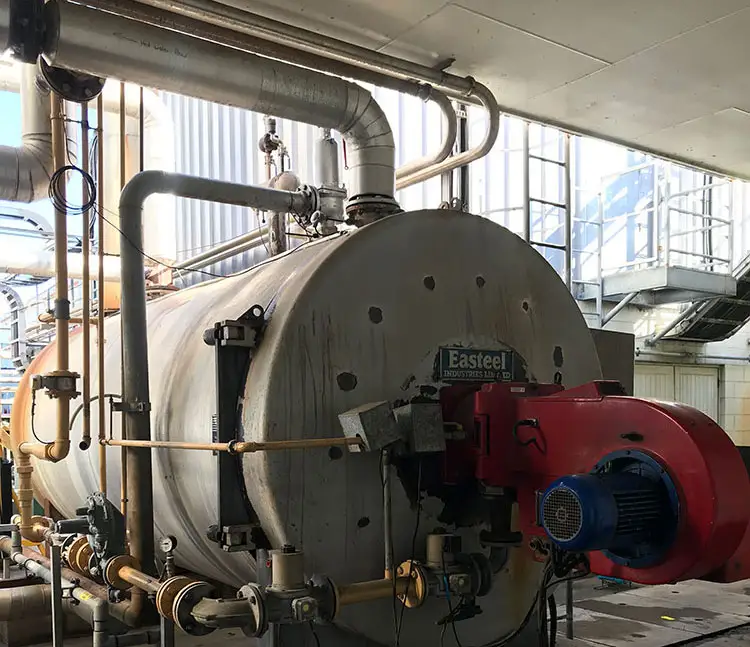
The site’s primary hot water boiler operates at full capacity and generates hot water for a number of processes in the factory including pasteurisation. The new heat pump will capture sources of waste heat and combine those through an ammonia heat pump to generate all of the site's secondary hot water requirements.
This energy-efficient process will result in a net decrease in energy consumption and will significantly decarbonise the site's process heat generation. It will also release 800-1000kW of energy back into the primary hot water boiler. The aim is to reduce natural gas consumption and cut emissions by 1,200t CO2/annum, or 25 percent of site CO2 emissions. The Longburn project is a pilot, and if it is successful there are plans to roll out heat pumps at other Goodman Fielder sites.
This project is not just about putting in a new piece of equipment. It’s about a shift in mind-set from the way we’ve always done things; from using a proven, trusted technology, to doing things in a new, more sustainable way.
“We’ve got a number of food processing facilities around the country that have significant refrigeration and heat loads which make this technology a potentially viable option. A successful rollout of the Longburn project (due to be completed in early 2022) will help to encourage the business to invest further in this technology and other alternatives to fossil fuels.”
This project is a small part of Goodman Fielder’s long-term sustainability plan.
“It ties in with our company's long-term sustainability strategy,” says Anderson. “We’re working on the Energy Transition Accelerator (ETA) programme with EECA to reduce reliance on fossil fuels over the coming years. We've moved to 100 percent renewable electricity across all our plants, offices and depots in New Zealand, and the overall ambition is for Goodman Fielder to be net carbon zero by 2040.”
Learn more about the Government Investment in Decarbonising Industry (GIDI) fund