The integration of the Burro autonomous electric vehicle represents a strategic shift toward energy-efficient, labour-optimised orchard operations for Cromwell-based orchard 45 South Cherries. The electric platform also provides a scalable, low-emissions alternative to traditional tractor-based systems.
Read about how the new technology is reducing diesel use and increasing efficiencies for the business.
Self-driving farm vehicles
Cromwell-based orchard 45 South Cherries is New Zealand’s largest cherry exporter, producing over 2,000 tonnes of cherries annually. The orchard’s operations span the entire horticultural chain — from growing and picking to packing and exporting. Each summer, the company ramps up from a permanent team of around 30 to more than 600 seasonal workers.
The self-driving Burro enables 45 South to reduce diesel use, enhance harvest speed, and reallocate human resources toward more skilled roles. Its modular control system, real-time localisation via GNSS and low maintenance profile make it a practical, future-focused asset for modern orchard systems, particularly high-density 2D trellis designs.
A compact powerhouse
At first glance, the Burro looks like a compact flatbed cart. But it's a high-tech, fully electric autonomous vehicle that can carry 500 kg, tow up to 2.2 tonnes, and travel at speeds up to 2.4 metres per second. A dual lithium-ion battery packs give it 8 to 9 hours of runtime on a single charge, depending on terrain and payload. Recharging is simple: just plug it in overnight.
For an orchard the scale of 45 South, where traditional tractors can burn through $25–$30 of diesel per row, the energy savings are substantial. Burros operate on electricity at around 90% lower energy cost and produce zero emissions on site.
“We don’t need a 3-tonne tractor just to move buckets,” says Mitchell Patrick, Orchard Manager. “Do that enough times, and you’re burning through thousands of dollars a year. “The cost and environmental savings are real.”
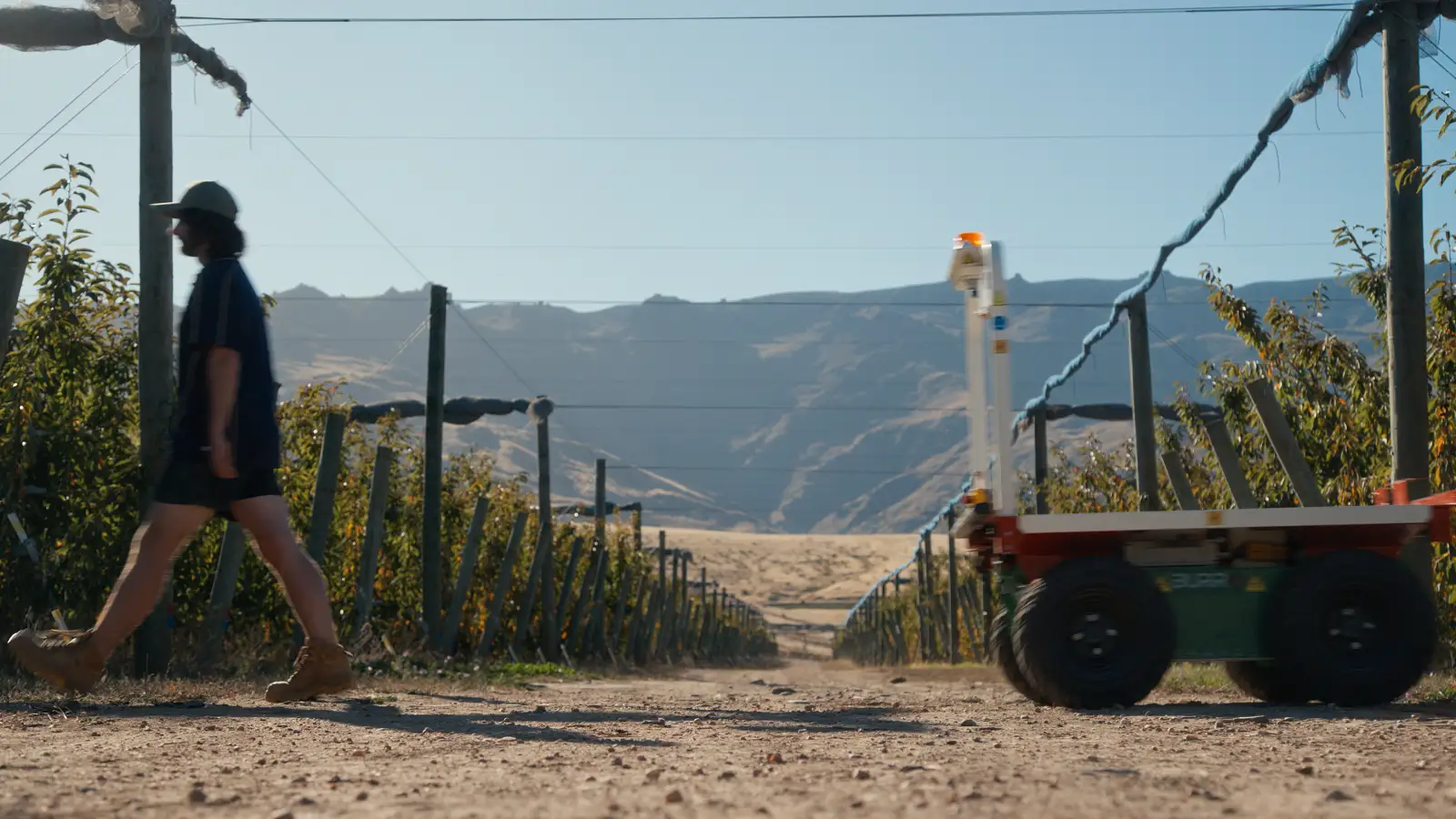
How Burro helped reshape orchard work
“Finding enough people — especially people trained for orchard work — is getting harder every year,” says Tim Jones, CEO of 45 South. “We realised we needed to either invest heavily in training or start reducing our reliance on labour altogether. It’s about improving efficiency and building a more sustainable business model — one row at a time.”
During peak harvest, pickers move thousands of buckets filled with cherries from the rows to the packing shed. It’s repetitive, time-consuming, and physically demanding.
This set the team on a new path to Burro, an electric self-driving vehicle designed to follow people, drive rows, carry loads, and tow equipment without a human onboard.
Rusty Davidson, Optical Technologies Manager at 45 South, was one of the first to try Burro in the field.
“Normally our bucket lifters carry four buckets at a time — two in each hand. Burro can carry 25,” Patrick says. “We used to need two or three lifters per row. With Burro, we often get away with just one.”
It was a game changer. Not only did it reduce the strain on workers, but it sped up the entire process. Buckets made it to the shed faster. Fruit stayed cooler, fresher, and in better shape for export.
This shift has not only improved productivity, but it’s also reduced workforce pressure, a major concern in an industry increasingly short on skilled seasonal labour.

An electric option that fits the orchard
At first, the team thought Burro would just be a handy tool for harvest. But the more they used it, the more they saw how versatile it was. Burro’s electric platform means less noise and lower running costs, all while allowing staff to focus on more complex or skilled tasks. The emissions are much reduced too.
“It’s perfect for those smaller jobs — things like spraying, towing, or even bird scaring,” says Mitchell Patrick, Orchard Manager. “You can just mount something on top and send it out to do the job. Day or night.”
Each Burro is packed with technology: a LiDAR sensor, front and rear cameras, a GPS unit, and multiple autonomous modes. It can follow a human operator, stick to rows using tree-tracking, or run entirely on GPS-mapped routes.
“The GPS mode is especially useful,” says Davidson. “You can map your rows on a computer or even drive them manually to train the Burro. Once you’ve set a path, it’ll follow it with crazy precision — like within a couple of centimeters.”
They’ve even outfitted one unit with better connectivity in areas with patchy mobile signal, enabling real-time GPS guidance in some of the most remote parts of the orchard.
Benefits of the Burro autonomous vehicle
The team at 45 South Orchards have found many benefits to their self-driving Burro vehicle.
- Labour efficiency — Significantly reduces manual handling needs during harvest, allowing smaller teams to move more fruit faster.
- Energy efficiency and electrification — Fully electric with all-day battery life, cutting fossil fuel use by up to 40% annually.
- Cost savings — Saves $25–$30 per hectare per pass in fuel costs, delivering ROI within 3–4 years.
- Autonomous functionality — Offers manual, follow-me, row, and GPS modes with high towing capacity and load handling.
- Workplace safety and quality — Improves safety and fruit quality through reduced fatigue, faster transport, and chemical exposure control.
- Scalability and versatility — Performs a range of tasks year-round with adaptable attachments, especially suited to 2D orchard systems.
- Operational independence — Simple to operate and maintain, freeing skilled staff to focus on higher-value orchard work.
Simple to use, easy to maintain
Despite all its tech, Burro isn’t difficult to operate. Basic tasks like following a person or driving up and down a row are intuitive. GPS-based functions take a little more training — but nothing out of reach.
“Once you get the hang of it, it just works,” Davidson says. “We’ve had a couple of flat tires, and some early battery issues, but our distributor sorted those right away. Otherwise, we’ve barely had to touch them.”
And the benefits keep expanding. This season, Burros are being tested for mowing, weed spraying, and UV disease prevention. A custom-built weed sprayer — designed in partnership with 45 South’s dealer, Agri Automation — now integrates directly with the Burro platform and fits the orchard’s layout perfectly.
“We’re still early days,” Davidson says. “There’s no full suite of attachments yet. But we’re working closely with the dealer to create exactly what we need.”
Reshaping the orchard — and the job
The biggest shift is how Burro is changing the day-to-day experience of orchard workers and managers.
“I used to spend hours on a tractor doing repetitive jobs,” Patrick says. “Now I can set a Burro up in the morning and spend my day on things that actually grow better cherries.”
It’s also changing how new technology is introduced to the team. Rather than reshaping operations around new machines, the team has worked Burro into the existing workflow.
While the Burro has brought clear benefits to orchard operations at 45 South Cherries, its implementation wasn’t without hurdles. The biggest initial challenge was setting up precise GPS mapping, which required detailed surveying of each row – a time-consuming but critical process for consistent autonomous operation. The orchard’s layout also introduced variability that required fine-tuning to get the best out of Burro’s navigation.
Training staff presented a moderate learning curve — manual and follow-me modes were intuitive, but GPS programming took time to master. Charging logistics required forethought too, with overnight recharging via standard outlets needing proximity planning.
Ultimately, integrating Burro successfully meant more than just plugging it in – it required rethinking workflows, reallocating labour, and embracing new systems. But with some patience and strategic planning, the team has managed to unlock real productivity gains.
Next steps
Looking ahead, 45 South is already designing new orchard blocks to better support electric and autonomous vehicles. That means straighter rows, 2D trellis systems, and ladder-free work environments — making orchards safer, more efficient, and easier to automate.
Jones says the team is energised by the new technology. “We’re not taking jobs away — we’re giving people better ones. It’s about moving with the times and using technology where it makes sense.”
Use of the Burro as given the team confidence to invest in more sustainable systems — electric, automated, efficient. 45 South see this as a long-term direction for the entire industry.
“We're showing what's possible,” Davidson adds. “Electric, autonomous tools like Burro aren't the future – they're already here. And they’re working.”
Advice to other growers
- Start small, scale quickly — Begin with one or two Burros focused on a clear, repetitive task – such as harvest transport. Train one operator well and build internal champions before expanding to multiple units or functions.
- Survey early, map precisely — For effective GPS navigation, businesses should plan for labour-intensive initial mapping, ensure clearly marked row entrances and consistent wheel paths, and invest in reliable GNSS coverage for remote areas.
- Invest in customisation — Collaborate with dealers or integrators to create attachments tailored to your block layout and crop type. Avoid waiting for off-the-shelf tools – many applications can be met with basic fabrication.
- Educate and empower teams — Burro’s UI is intuitive for non-technical users after initial training. Encourage staff to “play and learn” in low-risk scenarios (e.g. off-peak season tasks).
Read next
-
Solar on farms
Information, tools and support to help farmers install solar panels on farms in New Zealand.
- Innovation
- Solar energy
-
From sunlight to savings
A 54 kw solar PV system is paying off for this Wairarapa dairy farm.
- Case study
- Solar energy
-
Targeted spraying with drone technology
How an electric drone sprayer has helped Felton Road Wines reduce its diesel use and transform its vineyard management.
- Case study
- Innovation
- Solar energy