Things looked bleak for Whakatane Mill at the start of 2021 when it was announced that New Zealand’s only paperboard mill was set to close at the end of June.
The mill has been a vital part of the Eastern Bay of Plenty community since it opened in 1939. Its closure would have been devastating for the region, already suffering from the impact of the Whakaari/White Island eruption on tourism.
Thankfully, a group of investors could see the potential for the mill and the products it produced. Part of the commitment on buying the mill was not only to secure its future for its workers and the community, but also to invest in leading technology.
Accordingly, once the new ownership was confirmed, Whakatane Mill took steps to map a pathway, and invest in new technology that has significantly reduced its emissions and water waste.
Today, Whakatane Mill produces 150,000 tonnes of paperboard annually and runs 24 hours a day, 7 days a week. With over 170 people working at the mill, it is the biggest employer in the region and a significant contributor to the local economy.
The owners, the people who work here, their families and the local community all want to see Whakatane thrive and for the mill to be successful. That's a key focus for us and this project will help ensure the global competitiveness of the mill.
Tapping into local expertise
Reducing energy usage has been a focus for the mill for the last decade.
Whakatane Mill’s partnership with EECA has included energy graduates and energy audits which identified a number of future projects for the site. Also key to the journey has been support for the installation of a disc filter and related equipment (tanks, piping, pumps, etc.) to close the mill water loop, creating a circular system and increasing process temperature without using additional energy.
"We've worked in partnership with EECA and DETA Consulting on a number of different projects since 2016. We saw this project as an opportunity to change the way we operate and reduce our energy usage at the same time. It will also improve the quality of our product and our ability to service the market," said Jared McGregor, Chief Operating Officer, Whakatane Mill.
He says the project created work for the regional economy with locals building and installing the disk filter as well as the foundations and structure to house it, "We employ over 180 people, and following the upgrade we are now capable of producing 200,000tpa of board."
But the project was not without its challenges – many the result of supply chain issues stemming from the COVID-19 pandemic. The main piece of equipment, for example, took six months longer to arrive than expected.
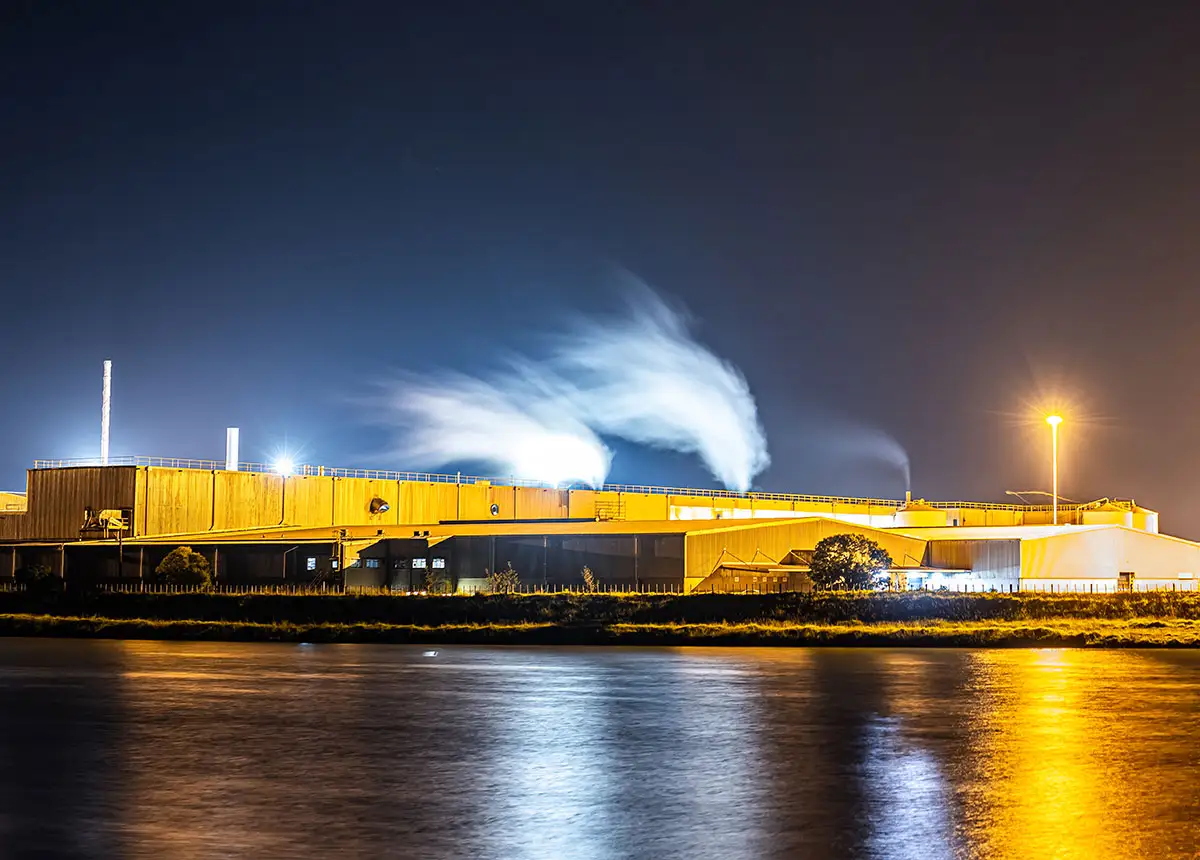
Less energy, less water, less waste
McGregor said a clean and clever focus makes sense for business.
“This project has improved efficiency for the mill. It means we don’t need to use our coal boiler to produce heat.
We are also drawing less water from the river so there is more available to the community.”
The subsequent temperature increase means water can now be reused in certain parts of the process – resulting in a range of energy, financial and emissions benefits, including:
- reduced energy-related carbon emissions by 21,612 tonnes per year
- reduced methane and CO2 emissions from landfill estimated at 3000 tonnes annually
- reduced wood and electricity consumption due to returning 4000 tonnes of fibre to the process instead of it going to landfill
- eliminating the transportation costs and emissions associated with sending the fibre to landfill
- significantly reduced water intake from the Whakatane River that can be used for crops and creating new regional job opportunities
- improved productivity, reducing fixed costs.
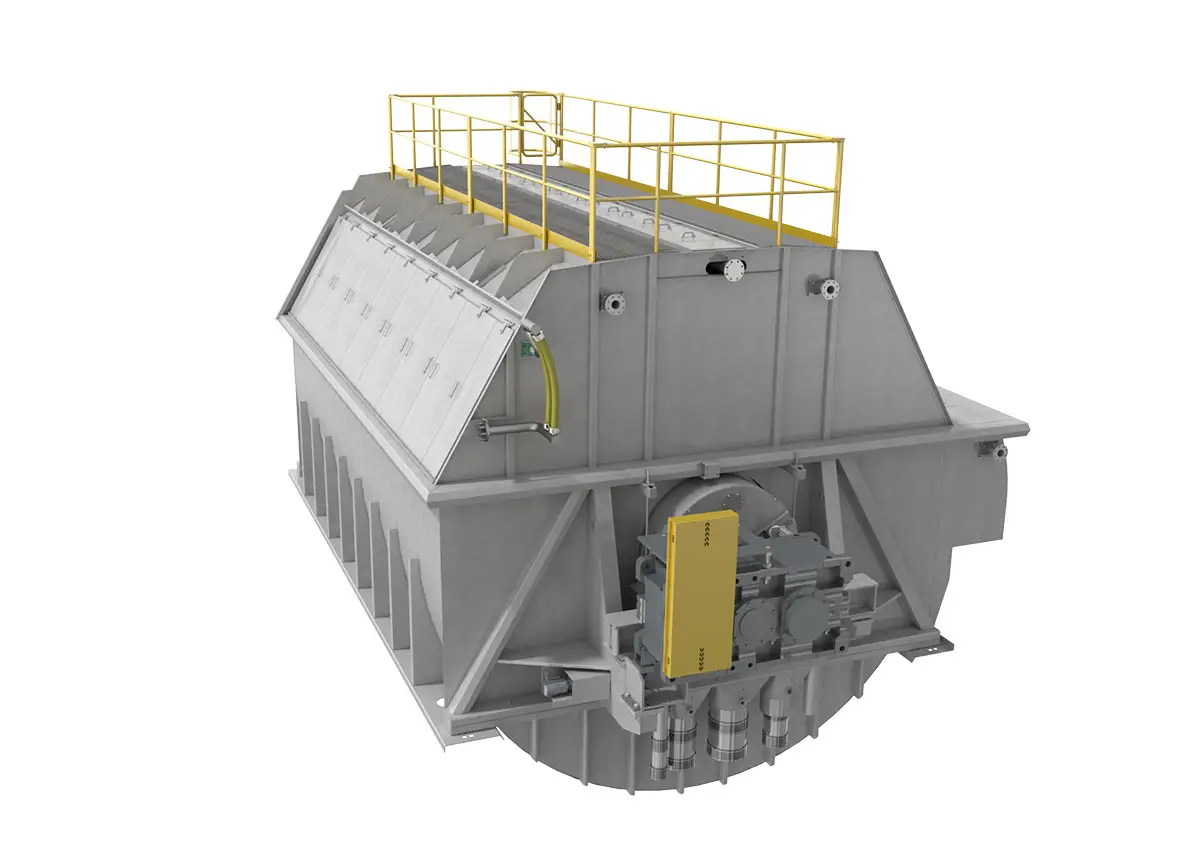
Post installation, the mill’s paper machine manager, Simon Tyler, said the team have already seen a significant drop in the amount of steam consumed.
“We measure steam in terms of tonnes of steam per tonne of board. To get that steam we burn gas. It means we are burning less fossil fuels to generate the energy we need and put simply, energy equals cash.”
Sustainability roadmap
The mill produces carrier board which is used for beverage, fast food and other products- basically packaging for anything you see in the supermarkets and shops.
“Previously if you bought soft drinks they were generally wrapped in plastic, and beer cans had plastic ring holders. Now most beverage manufacturers use our paperboard packaging," said McGregor.
“We want to operate in a sustainable manner and it is a key driver for our end users as well. Our customers are always looking for more environmentally friendly products. The world is moving away from plastic packaging, and we have a solution that uses renewable resources like wood and wood fibre to make our packaging.”
The company is looking at options to reduce emissions further and is working with EECA on options for its aging gas boiler for steam demand including a hybrid solution of biomass and electricity.
"With all these initiatives, the business performance improves, not just from a product and reputation point of view, but also in terms of operational efficiencies. They all tend to be aligned.”
-
WoolWorks leading the way in the wool industry
World-first decarbonisation of a New Zealand wool scouring plant.
- Co-funding
- Process heat
- Decarbonisation
-
Red meat, green energy
By switching to cleaner technologies, Alliance Group is helping reduce Southland’s carbon footprint.
- Case study
- Decarbonisation
- Process heat
-
Hot water, low emissions: Oceania is switching to renewables
Retirement and aged care living provider, Oceania, is upgrading to cleaner technologies in their facilities across New Zealand.
- Case study
- Decarbonisation
- Hot water