A fuel-switching project from New Zealand’s largest dairy cooperative has ticked all the boxes: eliminating carbon emissions, reducing costs, improving efficiency, and delivering multiple environmental benefits. All while improving bottom-line economic performance.
Business information
-
Company: Fonterra
-
Industry: Dairy manufacturing
-
Number of employees: 18,000-21,000
-
Site region: Waikato
-
Fund: Technology Demonstration Fund
-
Year of funding: 2020
Project summary
- Conversion of a 43 megawatt coal boiler to use wood pellets at Fonterra’s Te Awamutu dairy factory
- 98.4 per cent reduction in greenhouse gas emissions in this boiler, equal to 89,000 tonnes CO2-e per annum
- Significant reduction in particulate emissions
- Total project cost of $12 million
- EECA support of $200k through its Technology Demonstration Fund
About the journey
On 25 August 2020, Fonterra took a bold step in the use of renewable energy for milk processing at its Te Awamutu factory. A $12 million investment had been completed during the prior months with numerous COVID-19 restrictions in place, to convert the site’s 43 megawatt coal-fired boiler to an entirely sustainable, renewable source of energy – locally sourced wood pellets. EECA supported this project with co-funding of $200,000 through the Technology Demonstration Fund.
For the next seven months of the milk processing season the boiler ran continuously on a steady supply of wood pellets, reliably delivering 43 megawatts of steam to process 2.8 million litres of milk every day.
Benefits and insights
By switching to wood pellets and modifying the boiler to do so, the boiler’s thermal efficiency improved by approximately 4 per cent and carbon emissions from the boiler have been cut by 98.4 per cent – a reduction of 89,000 tonnes of carbon dioxide equivalent per annum based on the first year of operations using wood pellets. Sulphur dioxide emissions have also been reduced.
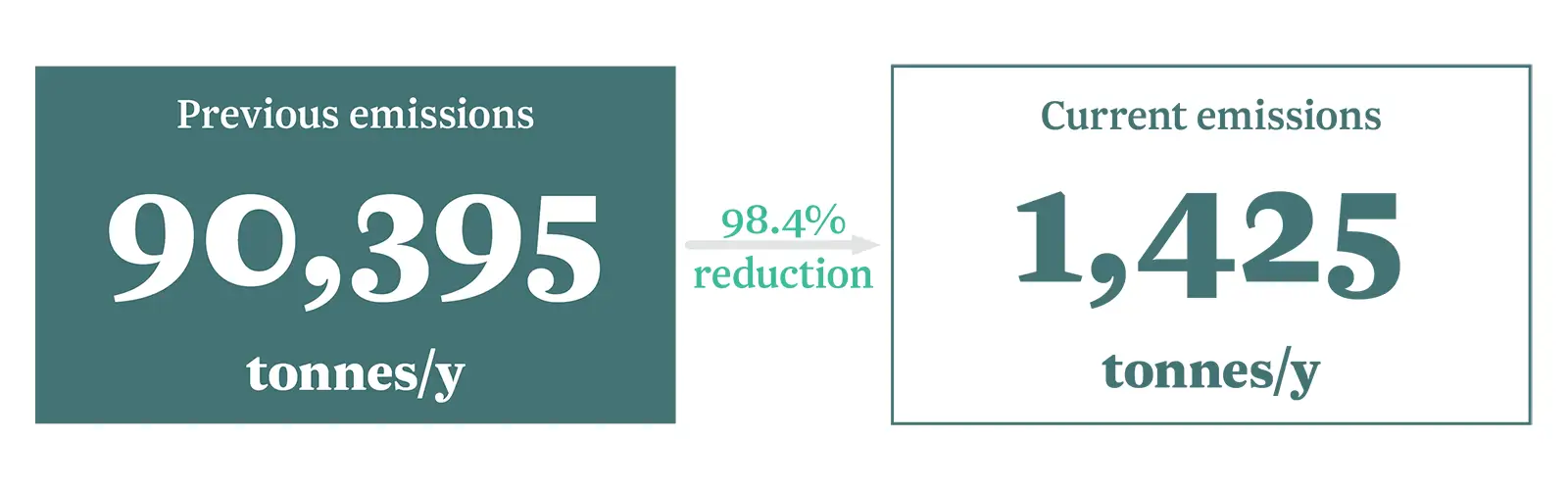
Kevin Liao, Fonterra's Senior Energy and Utilities Engineer, was the Commissioning Manager for the project. He says the project delivers on both environmental and financial outcomes.
"The use of wood pellets has cut both the rate and concentration of particulate emissions from the plant to less than 10 per cent of the currently consented levels, which materially improves air quality and should make reconsenting much simpler in the future," he said.
Additionally, whereas coal ash contains toxic chemicals, the organic wood pellets create an organic ash stream that is rich in potassium.
"This potassium is a valuable nutrient used to make potash which we are assessing for it to be recycled as a natural fertiliser for use on Fonterra farms," he said.
Kevin Liao said the Fonterra fuel switching project was a case study with much wider application for other energy intensive industries across the economy looking to cut carbon emissions and increase operating efficiency.
The use of wood pellets has cut both the rate and concentration of particulate emissions from the plant to less than 10% of the currently consented levels.
"The new fuel supply chain has been smooth and reliable thanks to a long-term supply contract with wood pellet manufacturer, Nature's Flame(external link).
"Changes required to the actual boiler itself were relatively modest. The main focus has been on boosting fan capacity in the boiler to increase combustion, improvements to the exhaust stack to capture fine particulates and covering the fuel reception area to keep the wood pellets dry.
"Unlike coal, wood pellets are hydrophilic and do not perform well when wet."
Operationally there have been a number of efficiency benefits in switching from coal to wood pellets. Whereas coal has approximately 30 per cent moisture content, the pellets contain just 10 per cent. As a result, the plant used to require seven to eight truck deliveries per day for coal, and now requires five to six for wood pellets.
The pellets are more uniform in size than coal, enabling delivery into the boiler to be more automated and consistent. Adjustments were required to conveyor belts carrying the pellets and a solution was required to manage additional dust from the pellets.
Looking to the future
Kevin Liao said while the fuel switching project stacked up commercially from the time it was commissioned, increasing carbon prices would increasingly advantage the wood pellet plant.
He said that additionally, the long-term domestic wood pellet supply chain looks positive as more and more forestry is being developed both to absorb carbon and deliver for the timber market.
As the world becomes increasingly concerned about climate change and the environmental impacts of the products they consume, Fonterra’s Te Awamutu project has shown what can be achieved with the right vision and commitment.
The plant is setting new environmental standards in a sector that has traditionally been viewed as difficult to shift to renewable energy sources. In doing so, it’s also future proofing the plant and delivering better economic performance for shareholders.
At a glance: Fonterra’s coal to wood pellet boiler switch
Performance outcomes:
- A 98.4% reduction in greenhouse gas emissions, equal to 89,000 tonnes CO2-e per annum
- The boiler has consistently and reliably delivered steam to the site
- Thermal efficiency of the boiler has increased by approximately 4%
- The current rate and concentration of particulate emissions is less than 10 per cent of the site's consented limited
- Sulphur dioxide emissions have been reduced.
Lessons learned:
- Wood pellet fuel must be covered for storage
- Pellets are more prone than coal to roll backward on steeper conveyors, requiring minor pitch adjustments
- Adjustments to boiler air supply are needed to enhance combustion
- Boiler grate temperatures could increase from fuel switching
- Dust can be an issue to manage with drier fuels such as wood pellets.
Final advice
Fonterra's Kevin Liao says the boiler conversion has been an important and big step for the company.
"This project has encouraged us and shown us what might be possible at other sites and operations. The conversion to wood pellet fuel has been hugely successful, it has made a meaningful impact and it has been such a satisfying and rewarding project to be a part of."
He encouraged any other business or operation considering a fuel switch conversion for their own process heat plant to start with a conversation with the original equipment manufacturer (OEM) and from there move to a desktop model.
"Our boiler OEM was very helpful during this process. All assets behave differently so the detailed conversation and upfront modelling will give you every chance of an efficient project and ultimate success."